Lean Maintenance
Nowoczesne podejście do utrzymania ruchu oparte na filozofii Lean pozwala znacząco ograniczyć przestoje i zwiększyć dostępność maszyn. Oferujemy kompleksowe wdrożenia TPM, CMMS, SMED i innych metod optymalizacji technicznej.
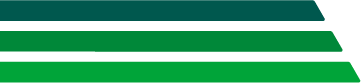
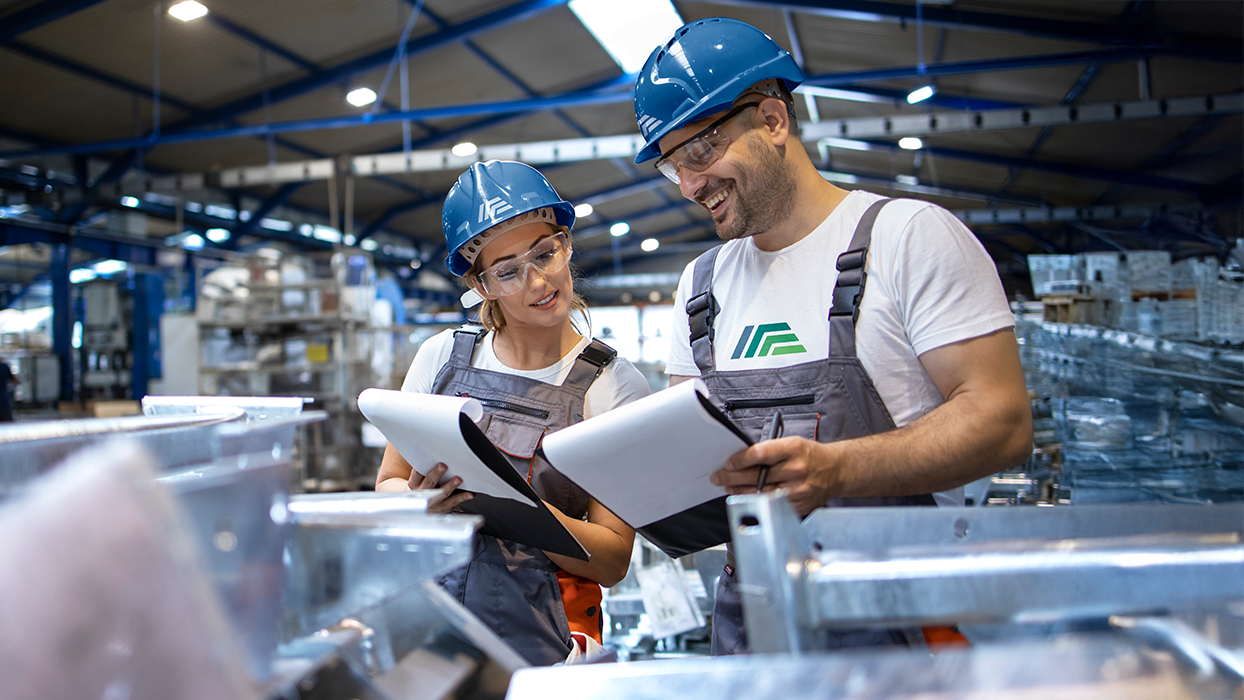
Lean Maintenance to nowoczesne podejście do zarządzania utrzymaniem ruchu, którego celem jest zapewnienie maksymalnej dostępności maszyn przy jednoczesnej minimalizacji kosztów operacyjnych. Wdrażane działania opierają się na eliminacji strat, usprawnieniu procesów serwisowych oraz wykorzystaniu zaawansowanych narzędzi analitycznych.
Kompleksowe usługi w zakresie Lean Maintenance, obejmujące wszystkie kluczowe obszary utrzymania ruchu, począwszy od audytów technicznych i optymalizacji procesów konserwacyjnych, po wdrażanie systemów informatycznych klasy CMMS oraz tworzenie strategii utrzymania ruchu. Dzięki zastosowaniu takich metod jak Total Productive Maintenance (TPM), analiza przyczyn źródłowych (RCA), redukcja czasów przezbrojeń (SMED) oraz cykl ciągłego doskonalenia (PDCA), możliwe jest znaczące zwiększenie efektywności operacyjnej przedsiębiorsw.
Usługi te są skierowane do firm produkcyjnych i przemysłowych, które chcą zwiększyć niezawodność swoich urządzeń, zmniejszyć liczbę awarii, a także zoptymalizować działania serwisowe i koszty eksploatacyjne. Działania prowadzone są zgodnie z najlepszymi praktykami zarządzania technicznego, międzynarodowymi standardami i indywidualnymi wymaganiami klientów.
Zespół specjalistów z wieloletnim doświadczeniem w obszarze utrzymania ruchu zapewnia wsparcie na każdym etapie realizacji projektu — od analiz i audytów, przez projektowanie rozwiązań, aż po wdrażanie i monitoring ich skuteczności. Celem jest stworzenie trwałych rozwiązań technicznych, które zapewnią ciągłość pracy, bezpieczeństwo procesów i optymalizację kosztów operacyjnych.
Wszystkie działania realizowane są zgodnie z najlepszymi praktykami Lean Management, międzynarodowymi standardami oraz indywidualnymi potrzebami przedsiębiorstwa.
Zwiększ efektywność utrzymania ruchu.
Audyty procesu utrzymania ruchu
- Analiza stanu obecnego systemu utrzymania ruchu.
- Ocena efektywności działań konserwacyjnych i naprawczych.
- Identyfikacja obszarów wymagających usprawnień oraz sporządzenie szczegółowego raportu z rekomendacjami.
Optymalizacja procesu utrzymania ruchu (VSM – Value Stream Mapping)
- Mapowanie strumienia wartości dla procesów utrzymania ruchu.
- Identyfikacja wąskich gardeł, strat oraz zbędnych operacji.
- Projektowanie i wdrażanie usprawnień zwiększających efektywność procesów konserwacyjnych i naprawczych.
Total Productive Maintenance (TPM)
- Wdrażanie programu TPM w celu zwiększenia dostępności maszyn i urządzeń.
- Szkolenia dla zespołów produkcyjnych w zakresie autonomicznej konserwacji.
- Ustalanie harmonogramów prewencyjnych oraz wdrażanie systemu ciągłego doskonalenia.
Strategie Utrzymania Ruchu:
- Opracowanie i wdrażanie strategii konserwacji prewencyjnej, predykcyjnej i reaktywnej.
- Tworzenie dynamicznych harmonogramów obsługi technicznej.
- Dostosowanie strategii do specyfiki zakładu produkcyjnego oraz wymagań technologicznych.
Dobór i implementacja systemów klasy CMMS
- Wybór odpowiednich systemów do zarządzania utrzymaniem ruchu (CMMS – Computerized Maintenance Management Systems).
- Konfiguracja systemu i jego dostosowanie do indywidualnych potrzeb przedsiębiorstwa.
- Integracja z istniejącymi systemami ERP i automatyki przemysłowej.
Analiza, wdrożenie i optymalizacja kluczowych wskaźników efektywności (KPI)
- Definiowanie wskaźników KPI, takich jak OEE, MTTR, MTBF, dostępność maszyn i efektywność prac konserwacyjnych.
- Tworzenie raportów analitycznych oraz dashboardów monitorujących postępy w czasie rzeczywistym.
- Wdrażanie działań korygujących w celu osiągnięcia zakładanych wyników operacyjnych.
Elastyczne zarządzanie zmianą w Utrzymaniu Ruchu (PDCA, RCA, SMED)
- PDCA (Plan-Do-Check-Act): Zarządzanie cyklem zmian w procesach utrzymania ruchu.
- RCA (Root Cause Analysis): Analiza przyczyn źródłowych awarii i ich eliminacja.
- SMED (Single Minute Exchange of Die): Redukcja czasów przezbrojeń maszyn.